Load Banks
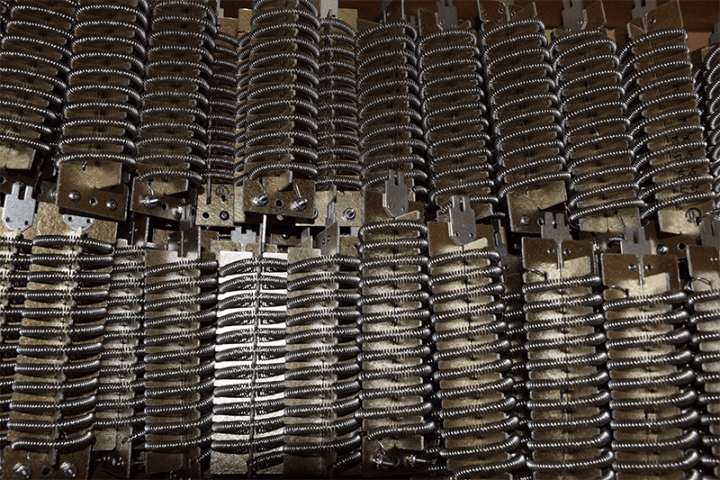
A load bank creates resistive electrical load for testing, discharging and recycling processes. It applies a load to an electrical power source and dissipates the power as heat. Ambient air-cooled load banks (the most common type) are like giant hair dryers. When activated they can handle large power loads in a controlled manner.
What is a Load Bank Resistor?
Load banks are powerful heating elements that form a network of resistors absorbing an electrical load from a generator, battery, or other power sources. A poorly designed load bank element leads to sagging, shorts, inaccurate data, and a reduced lifespan.
TUTCO Farnam understands the need for a reliable Load Bank solution. All TUTCO Load Banks are reliabily engineered with custom open coil heating elements. Quality and durability are required for applications such as emergency back-up, UPS, inverters, generators, data centers, energy turbines, and production line testing. All Load banks use custom innovative designs based on application and required power ratings. Tutco-Farnam only uses top-grade alloys for load bank element resistors. From single handle enclosures to 20’ containers, Load banks can be custom-designed and manufactured to your specific application.
Load bank manufacturers today are responding to demand with units that are more compact, integrate with other systems, offer better controls, and meet tougher environmental regulations. We tackle some of the toughest electrical, control, and physical space requirements with our unique designs. Do you see room for improvement with your resistors? Better response? Longer life? Do you have tough space requirements? Do you need something better suited to your airflows? Decades of custom heater design experience await your next project.
Tell us about your project in our detailed contact form.
What is the Purpose of a Load Bank?
The purpose of a load bank is to either add a controlled electrical load to a situation as in the case of ‘wet stacking’ prevention or to simulate electrical loads normally created by other units such as servers. They mimic the “real” load that a power source will see in a real-world application. A load bank provides a contained and controllable load, which is different from an operational load that is likely to have random qualities and be less predictable.
There are many applications but most fall into one of the following camps. In power source testing an operator is testing power sources like generators and UPS units. Load testing is performed on all new generators and it pops up again over time as part of routine maintenance. Load banks help to ensure that power generation can support loads with their intended voltage and frequency requirements. Autoload sensing is another big area. The load bank is sensing whether or not it should step-up, step-down, or turn off. One common application is to keep a diesel engine from continuously operating below a certain threshold as one or more simultaneous loads get turned off.
Where Are Load Banks Used?
Load banks are used in many places for a variety of purposes:
- In and on buildings as part of power generators (Gen-sets)
- Emergency back-up for critical situations such as hospitals
- Testing constant current regulators in high power situations
- In industrial and test lab environments
- Commissioning power systems
- Battery testing
- Direct substitution of a computer, modem or server to simulate heat and power loads
- Assisting with server placement in data rooms
- Testing and verify HVAC capacity in large data centers
- NFPA 110 testing requirements
- Testing both long and short-term
- Research and Development
Types of Load Banks
There are three main types of load banks.
- Resistive: Absorbs a load (most common type)
- Reactive: Inductive (lagging power factor) and/or Capacitive (leading power factor)
- Resistive/Reactive: Combines both in one package. Used in solar and wind energy.
All three types come with a wide variety of options and configurations that can be rented or purchased. Custom machines are often made to better simulate a piece of equipment or to be more useful in a particular situation.
What Are the Main Parts of a Load Bank?
The main parts of a load bank include…
- The resistive and/or reactive components
- The blower (needed to remove the heat so it doesn’t burn up)
- Controls and metering, which may be analog or digital
- Connectors
- System protection
- The enclosure
The open coil heating element is at the heart of the resistive load bank. Longevity, stability, environment, airflows, safety, and control are all factors carefully considered when developing a load bank resistor. At Tutco-Farnam experienced and highly skilled air heater engineers attend to every facet and requirement from material selection to long term serviceability. Some of the more ‘heating element’ specific considerations include:
- Element physical design
- Patterns and frames (eg. rack, circuit layout)
- Space restrictions
- Air flows and pressure
- Material choices
- Wear, tear and corrosion resistance
- Primary support design and materials
- Test for ‘Sagging’ reduction opportunities
- Eliminating weak points
- Good windings and stable supports
- Easily serviceable
- Any client-supplied project requirements
Load Bank resistors are designed specifically for the type of load bank they will inhabit. When it comes to performance, material and engineering choices are what make the difference.
The blower helps to remove the heat from the heating elements and is critical for effective and safe performance. Most units will shut-down or dump their load if no airflow is detected. Airflow patterns are either side to side or bottom to top. The air coming out can be very hot so it is best to look ahead of time to make sure there isn’t something obstructing either end especially if it is flammable or something living. You don’t want a giant horizontally blowing load bank dumping its hot air directly into pedestrian traffic.
Some interfaces have simple toggle switches that the operator physically flips on/off to step a load up or down. On/off and fault indicator lamps provide feedback. Banana plugs may be available for attaching voltage and current meters. Other systems may be digital, integrate with a laptop or even a building’s monitoring system, control multiple load banks, log data, and provide detailed reports. A display might be simple analog meters, touch screen digital displays, or even a laptop.
Load bank enclosures run the gamut from manageable boxes carried in one hand to behemoths that can fill a flatbed. Some are meant for indoor use while others are specifically designed and rated for continuous use outdoors. Materials used to make a load bank enclosure may include...
- Steel
- Aluminum
- Aluminized steel
- Galvanized steel
- Hot-rolled steel
- Heavy gauge
- Folded/welded
- Double skinned
- Stainless steel heat shields
- Rubber gasket seals
Enclosure coatings vary. Some are coated with a polyurethane enamel while others may be primed and painted w/ UV resistant polyurethane.
Stationary units are usually mounted on concrete pads next to a generator, are intended to run at a particular voltage, and do one thing very well. Portable units come in all sizes and typically have more versatility built into them to be used for various applications in varying conditions for both field or production line testing. A few portable options to consider include...
- Handles for carrying small units by hand
- Sturdy protective case
- Casters (swivel, fixed, locking)
- Forklift channels
- Lifting eyes
- Tie-down hooks
- Mounted to a highway safe trailer
- Mounted to a vehicle or flatbed
- Ability to mount multiple units in a row on the same bed
Connectors may include...
- Cable set
- Terminal blocks
- Plugs
- Twist plugs
- Quick Connect Camlocks
- Detachable line cord
- Cat-5/RJ-45 connectivity
The most basic safety features will include circuit protection with fuses and/or breakers. Emergency stop/disconnect switches and possibly branch circuit fusing on all load steps may be included. Other protections may include...
- Fan fail, over temp, over-voltage, etc.
- Voltage sensing relay protection
- Wrong voltage protection
- Cooling air loss protection
- Disabled if access doors are open
- Motor overload protection
- Fan requirement before element can to take a load
- Autoload dump circuit
- Operating fault log
- Faults automatically disconnect unit as necessary
- Internal temperature monitoring
- Protections at inlets and louvers
Load Bank Considerations
The following are a few things (features and concerns) to consider when buying, renting or hiring someone to build your next load bank...
- The life expectancy of heating elements
- Serviceability of heating elements
- Overall heating elements and suspension system design
- Large easy to read interface (meters, LCD, etc.)
- Number of technicians needed for field testing
- Cool-down period required
- Compatibility with tools such as a multimeter
- Over-temperature protection
- Weight/portability
- Voltage, Current and Frequency monitoring
- Range of voltages
- Single and/or 3-phase
- Element temperature rating vs allowable load
- Longer lasting and little to no cool-down when operating less than half of temperature rating.
- Isolation of components from resistive elements
- Operating noise/blower noise
- WiFi-enabled
- Blower motor horsepower
- Number of load steps and load step resolution
- Multi-channel that can operate at independent voltages
- Number of load steps per channel and load combinations
- Fine-tune control of airflow and ability to compensate for altitude differences
- Rubber support feet
- Comfortable heavy duty carry/lift handles
- Rated for continuous operation
- ISO9001 quality
- Emission standards
- Ease of operation
- Does it fit through doorways and elevators
- Extreme cold weatherization
- PC based control and monitoring
- Real-time data acquisition and logging
- Ability to generate reports
- Long-distance remote operation
- Heater strip within the load bank to minimize moisture and condensation
- Software to assist with Tier IV testing
- Shipping protection
- UL, CSA, CE
- Remote control
- Trailer mounted ready for highway travel
- Trailer capacity to carry additional equipment
- Serviceability of unit
- Weatherproof exhaust hoods
- Load step resolution
- Cords, plug assemblies
- Mounting hardware
