Heat Staking Heaters
Heat staking heaters provide heat to the business end of heat staking equipment. Precise and reliable thermal control is critical in any heat staking process. This is especially the case with glass-filled plastics. Too cold and you get deformations and cracks. Too hot and you get sticking and rough edges. The boss size also presents temperature control restrictions. Larger pins are tougher to heat than small pins. It’s all about temperature control, reliable heat, and timing. Tutco-Farnam supplies rugged open coil heaters to equipment manufacturers, OEMs and end-users. Our Heat Torch line of compressed air heaters provides reliable repeatable results while our Cool Touch option allows safe direct handling of the heater body. We help you to achieve high production standards, tight assemblies, stress-free joints, and attractive product surfaces with our line of durable heat staking heaters.
What is Heat Staking?
Heat staking (also known as thermoplastic staking, thermostaking, thermal staking, and hot air/cold staking) is a method of permanent-joint assembly. The process involves heating and compressing a plastic peg (stud or boss) so as to soften and deform it in a controlled manner after it has been inserted through a hole. Hot air is commonly used to heat the boss above the glass transition temperature. A staking punch is then used to compress the peg, squishing it into a new shape, mechanically locking the two (or more) pieces together. The plastic should then be cooled down below the glass transition temperature while under constant pressure to ensure a good joint.
Heat staking joints are commonly found in consumer appliances, automotive body parts, medical devices, IT, and telecom components. Modified versions of this process are used for embedding threaded inserts and stamping dates. Heat staking can also be used for disassembly in recycling processes or when reworking an assembly. Some of the most commonly used plastics are acetal, polyamide, acrylonitrile butadiene styrene (ABS), polystyrene (PS), polycarbonate (PC), polypropylene (PP) and glass-reinforced nylon (GFN).
The right combination of heat and pressure for the application is critical. The type of plastic, diameter, height, geometry, and the number of simultaneous compressions are all factors that affect the process and ultimate strength of the joint. The surrounding product's sensitivity to damage is yet another consideration in your process. Reliable controlled heat is foundational and a quality heat staking heater will help to deliver strong consistent assemblies.
Heat staking machines range from basic hand operated bench-top arbor presses to complex high-tonnage fully automated production machines. While some machines are designed with versatility in mind, many of these machines are engineered for a specific production task. Tutco-Farnam works within your project requirements to improve performance, production, longevity, accuracy, and reliability.
The possible features of heat staking machines are many:
- Sophisticated process control
- Part sensing
- Multiple embedded temperature controllers
- Auto-tuning
- Digital timers
- Pneumatic thrusters
- Slide tables
- Touch screen
- Password protection
- High-quality servos
- Safety guarding
- High-pressure presses (for large parts and multiple simultaneous staking locations)
- Custom tooling options
- Quick tooling changeout
- Resilient finishes
Advantages of Heat Staking over other joining processes:
- Fast
- Economical
- Repeatable
- Consistent
- Join different materials...
- plastic to plastic
- plastic to non-plastic (e.g. metal, glass, PCB’s)
- join two non-plastics
- Eliminates the need for rivets and screws
- Accurate control, small process window
- Simple mechanisms
- Lower cost machinery
- Multiple fastening points
- Higher density welds
- Can handle some difficult to weld plastics
- Integration with other automation technologies
- Many different sizes and shapes including flared, spherical, hollow, knurled, and flush (or countersunk).
- Captive stakes are useful to hold something within a plastic housing.
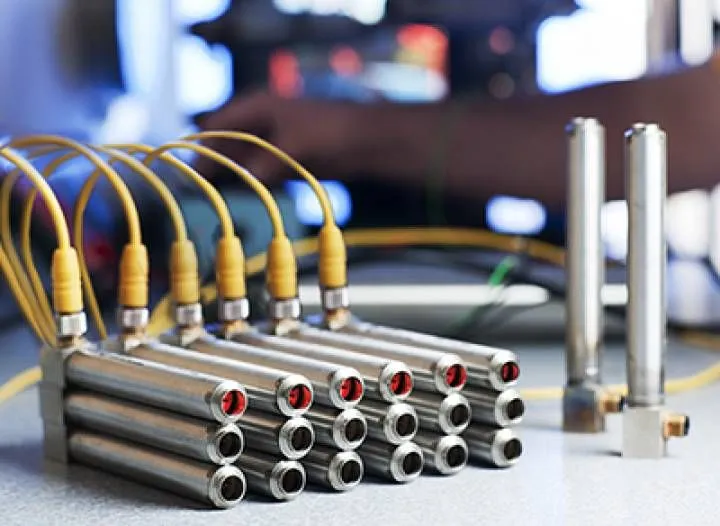
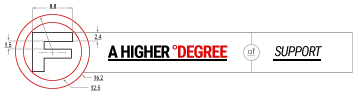
Engineering service and support is a big part of what we do. Offered on an application by application basis. With over 2,000 unique heating element designs, chances are we have done something similar to your project.