We've got a new website! Please let us know if you encounter any issues. Email us at info@farnam-custom.com, your feedback is valuable.
Gas Chromatograph Heaters
Gas Chromatograph operators want greater speed, accuracy, sensitivity, and portability from their analytical equipment. Temperature control plays an increasingly important role as equipment evolves to meet demands. At the heart of temperature control are the heaters and control systems that regulate a tiny sample of material as it traverses and separates along a column. The temperature of a sample being analyzed is a fundamental variable that the operator seeks to control. Small deviations will have large effects on data quality and usefulness. Dialing in the column temperature supports many of the improvements operators seek and is a priority for OEMs who want to remain competitive. Innovative heater design is a key element at the heart of next-generation equipment. Tutco-Farnam has decades of experience designing and manufacturing custom heaters for sensitive analytical equipment in the laboratory, medical & oil/gas industries. We help operators achieve greater speed and accuracy with robust thermal designs. Our heaters tightly control column temperature with uniform consistency from run to run. Contact a representative today and see what Tutco-Farnam can do for you.
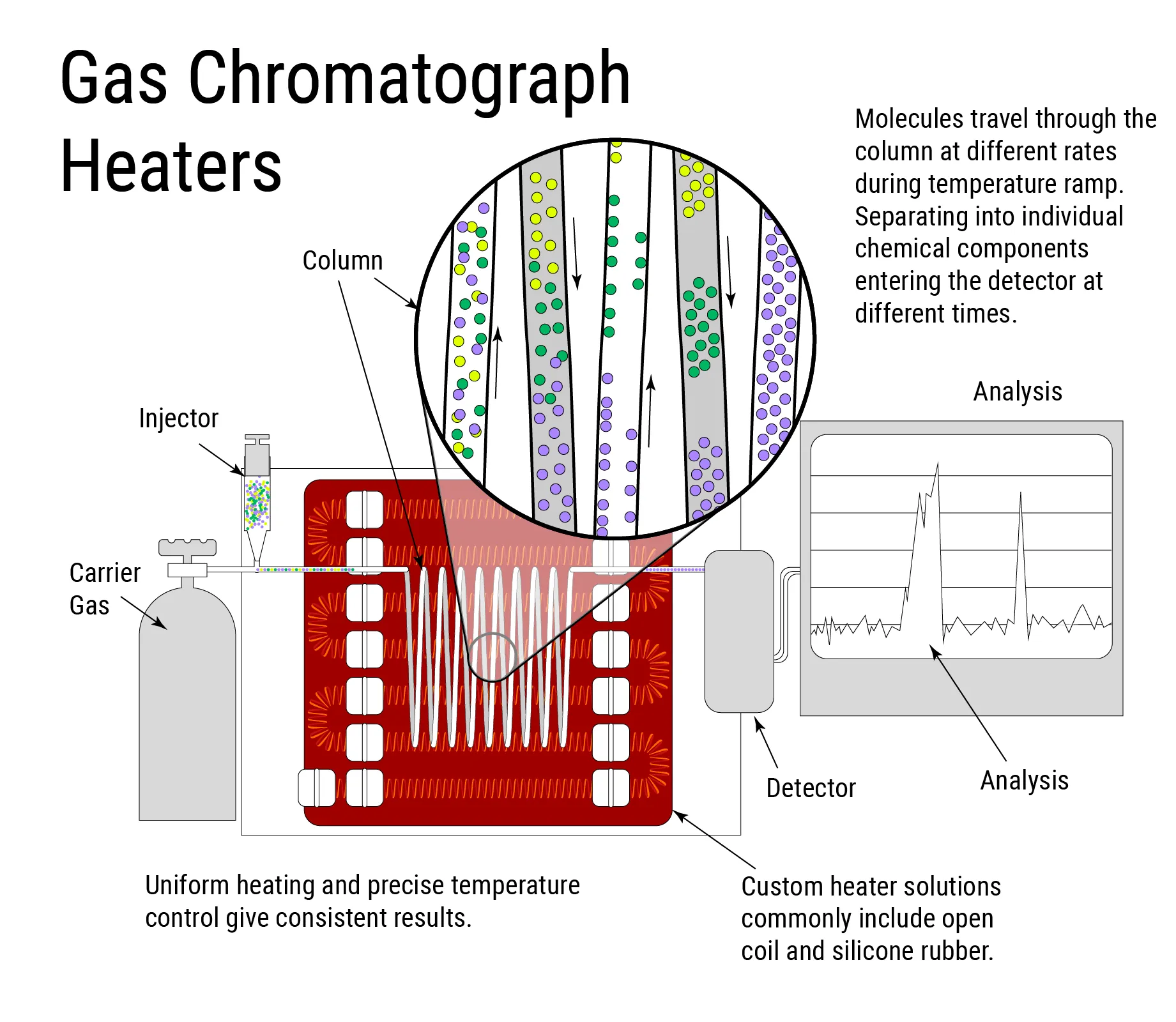
What is Gas Chromatography?
Gas Chromatography (also called GC) is a separation technique. It is a method of separating a mixture or sample into individual chemical components. The goal is to isolate all of the relevant compounds of interest so we can achieve individual chemical identification. While a gas chromatograph will not tell us precisely what each particular element is, we can infer the outcome by coupling our data with expected results. We then identify those to which there is a high degree of probability that a certain element exists.
A Gas Chromatograph is the core piece of equipment used in Gas Chromatography. It is often used in series with another piece of equipment such as a mass spectrometer. A gas chromatograph is an analytical device consisting of a long thin coil tube called a column, which is enclosed in a temperature-controlled space. Material enters the column by way of an injector and exits the column into a detector. The sample material is carried through the column in a carrier gas.
The material being sampled separates into constituents due to an affinity that each part has to material within the column. The special substance used in these columns that helps to separate a sample into its components is called 'Stationary Phase'. It is usually a very high molecular weight liquid. Material is absorbed into the stationary phase and desorbed back into the carrier gas stream repeatedly as it traverses the column. Some components will spend less time in the stationary phase while others will spend more time. This adsorption and desorption drive the separation process.
What are Gas Chromatograph Heaters?
Gas Chromatograph heaters are designed to provide highly uniform temperature across the length of the column. This precision allows the operator to capture sample data with resolutions that are useable and repeatable from run to run. Small changes in column temperature and unstable temperature gradients can have a significant effect on elution times resulting in poor and unusable data. Gas Chromatograph heating elements are designed to ramp and hold the temperature of a column within a very small margin of error.
Retention time is the amount of time a compound exists in the column. A lack of column temperature uniformity will affect retention time. This is seen on a Chromatogram as the time from the sample entering the column at time zero to a ‘peak’ usually seconds or minutes later. After separation each compound is going to spend a different amount of time in the column, hence the different peaks on a gas chromatogram. No matter what heating method is used (ie. isothermal or programmed), any fluctuations along the column during sample analysis are going to have a significant effect on retention times.
Heating the Column
The chromatograph operator establishes a temperature profile based upon variables that include the column (type & size), carrier gas, flow rate, and the material being sampled. The operator relies on the chromatograph to provide precision temperature control during the execution of a thermal profile. The temperature control system is designed to support a unit's intended purpose. Units that handle a wide diversity of columns require thermal control designed for that flexibility. Other column temperature control considerations include maximum limits, bleed, and contamination.
Max Limits: Operators are cautious not to exceed maximum column temperatures as the stationary phase of each column has its own unique temperature limitation.
Bleed: All stationary phase columns experience some amount of column ‘bleed’. Operatures seek to limit bleed as it adds background noise to the data and makes it harder to quantify. Bleed is noise that comes from the phase itself slowly leaving the column and registering in the detector. Higher temperatures as well as thicker film phase will result in greater column bleed.
Contamination: Columns are purged ahead of sample testing so that no previous sample contaminants or oxygen are present in the tube. A column heated above certain temperatures with the presence of oxygen will damage the column. Columns should never be heated without the flow of carrier gas.
Temperature Programmed vs Isothermal Elution
For most analysis, a temperature ramp is programmed that starts when the sample enters the column at a lower temperature and increases in a precise manner to a higher temperature. This is called Temperature Programmed Elution. The ramp is linear and requires a heating system that is powerful enough to maintain a linear temperature increase from injection to final elution. At the beginning of the ramp, most of the compounds are not moving very much if at all. As the temperature increases, one of the stationary compounds will start moving. Then another. This highly controlled increase in temperature helps to improve sample separation while minimizing analysis time.
A sample run may also involve a single set temperature for the entire column. This is called isothermal elution. The column is heated to the set temperature prior to the sample entering the column. The use of a single set temperature is used with ‘packed’ columns though altogether less common. The shared purpose of these column heating technologies is to produce thermal conditions that yield the best component separation in a reasonable amount of time. The operator's job is to optimize the column parameters.
Convection Oven
Columns are commonly heated by a custom convection oven using electrical resistance heating elements. These may be in the form of open coil air heaters, flexible heaters like silicone rubber and polyimide film, or some combination. A fan rapidly moves the air within the oven to smooth out temperature gradients and drive thermal uniformity. Insulation minimizes the differential between the inside and outside temperature of the oven. These ovens are engineered and finely tuned for their specific purpose.
Heater-Column Assembly
Another method uses a heater that spans the length of the column in very close proximity to the column. The entire heater/sensor/column assembly is encased inside another tube. This can be very accurate but also increases column replacement cost as the column and heater become inseparable. Another version of this involves the column being etched into flat material. Heaters are then attached. Still another version combines the traditional oven with the heater-column assembly.
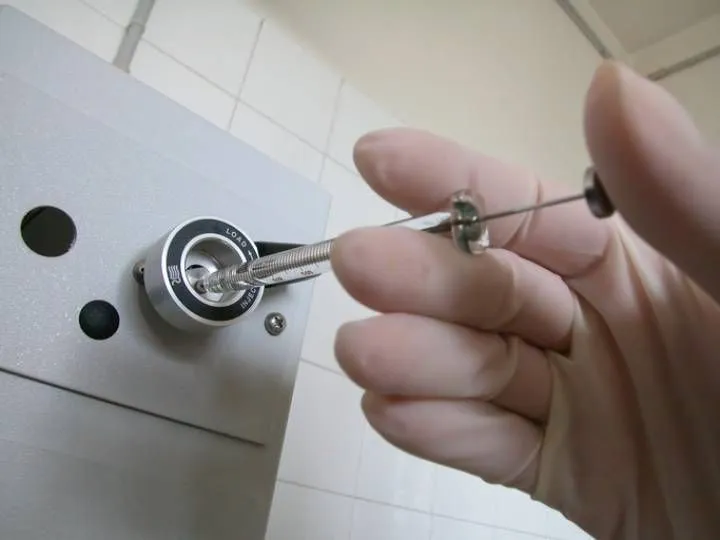
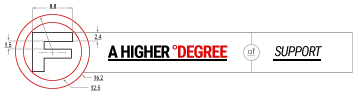
Engineering service and support is a big part of what we do. Offered on an application by application basis. With over 2,000 unique heating element designs, chances are we have done something similar to your project.